世界中のライダーに支持されるブランド「フィジーク」。その本拠地であるイタリアはポッツォレオーネの本社を訪れ、製造の現場と開発の思想に触れてきた。熟練職人の手仕事から最新3Dプリント技術まで──現地取材で見えた“フィジークの本質”をレポートする。
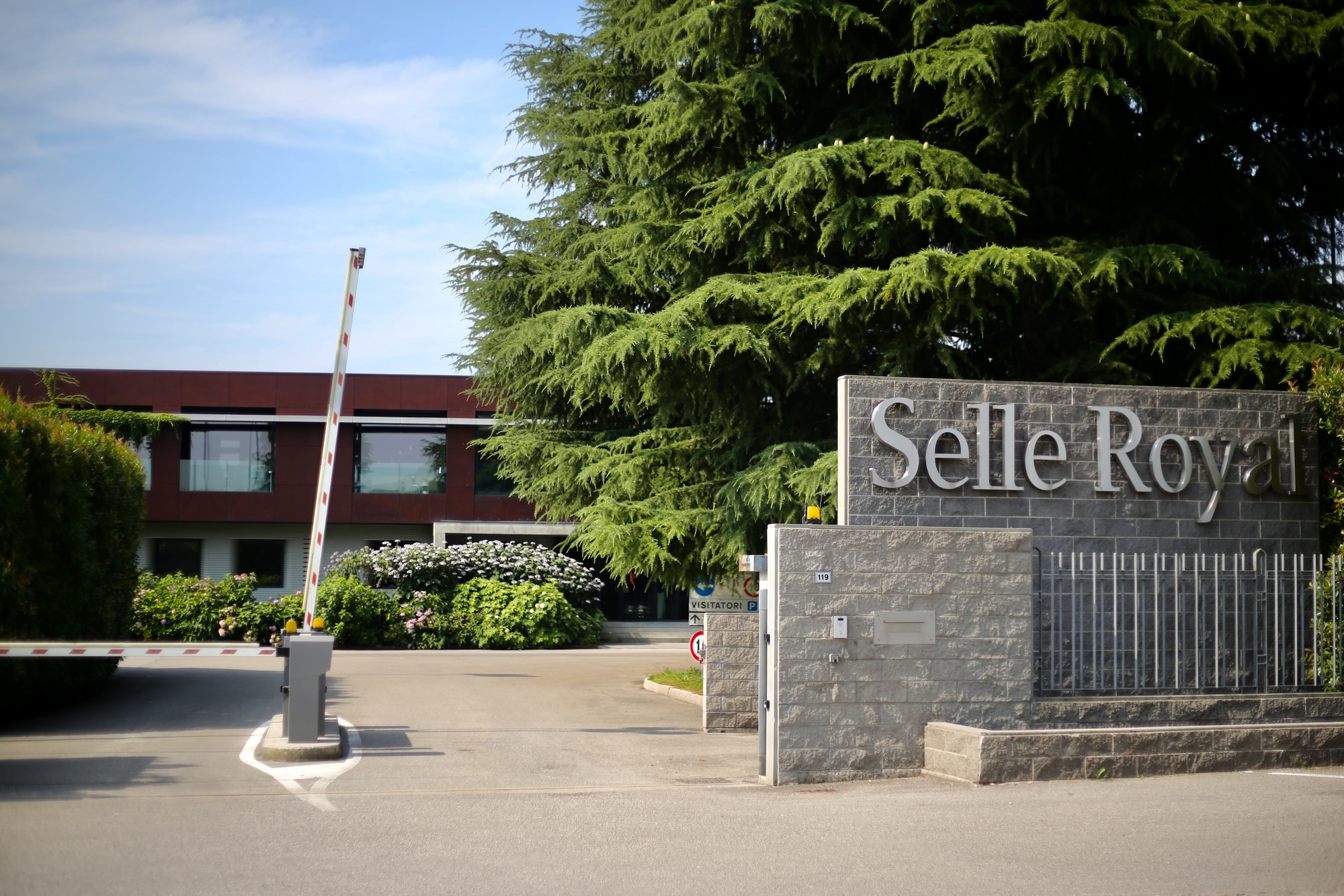
ヴィチェンツァ郊外の町、ポッツォレオーネにあるセラロイヤル本社。フィジークのサドル製造拠点でもある photo:So Isobe
イタリア北部、ヴィチェンツァ郊外の町、ポッツォレオーネ。名だたる名門ブランドがひしめくヴェネト州に、世界中のライダーから愛されるブランド「フィジーク」、そしてその親会社であるセラロイヤルグループの本社はある。
周囲に広がるのは、穏やかな農村風景と点在する工場群。高い建物はほとんどなく、空はどこまでも高く広い。訪れたこの日も、ヴェネト平野らしい開放感に包まれていた。
セラロイヤルの原点は、1956年にリッカルド・ビゴーリンが立ち上げた小さな自転車サドル工房にある。それから約70年。いまや同社は、年間1400万個以上の製品を手がける世界最大級のサドルメーカーへと成長した。ポッツォレオーネは創業当初から変わらずブランドの中枢を担い、現在は本社機能と開発部門、さらにフィジークの高性能サドル製造を担う主要ファクトリーが集約されている。
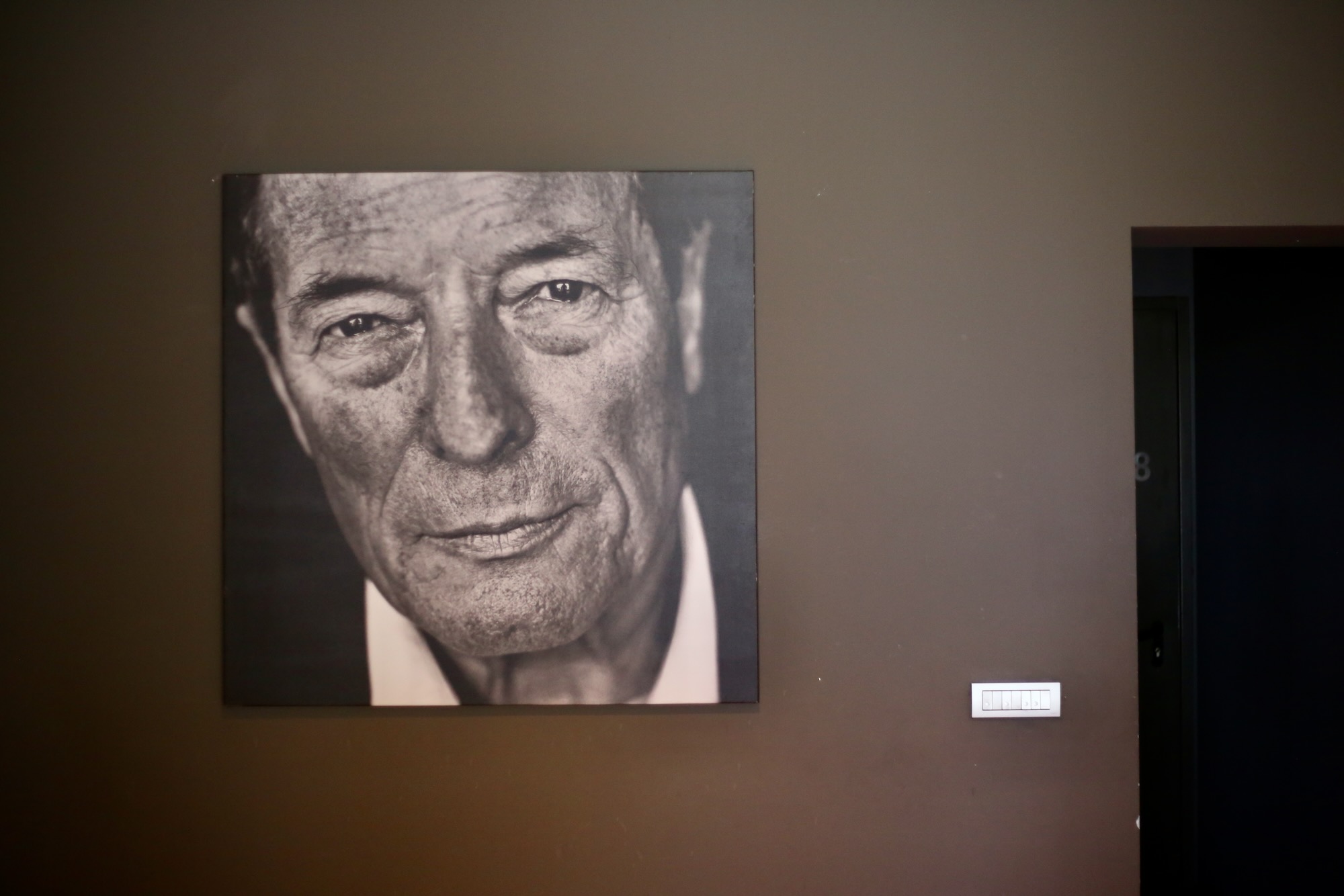
エントランスに掲げられた創業者リッカルド・ビゴーリン氏の写真 photo:So Isobe 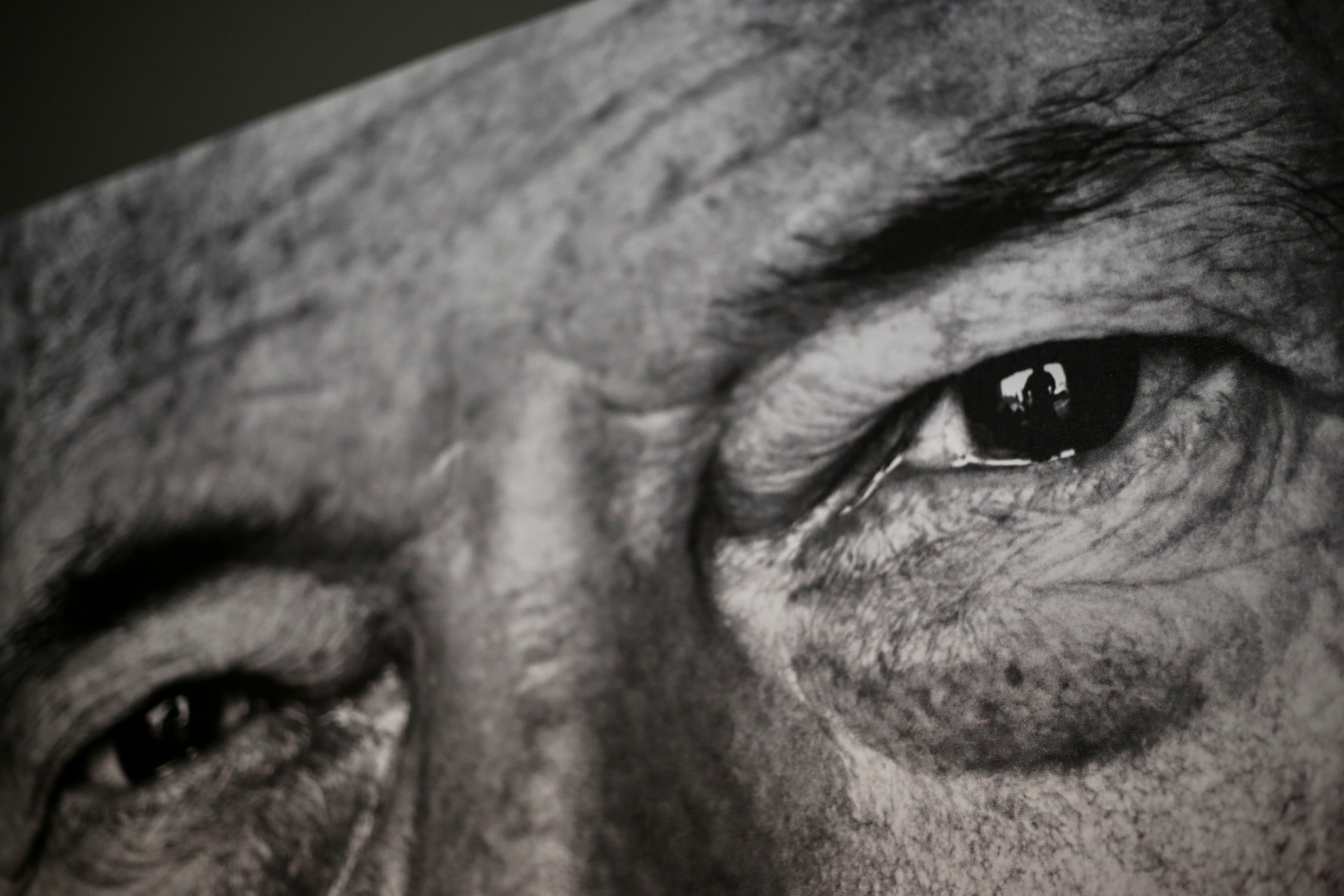
彼の瞳に映るのはライダーの姿。セラロイヤル、そしてフィジークは創業以来ずっと、自転車と身体の「接点」となる製品を作り続けてきた photo:So Isobe
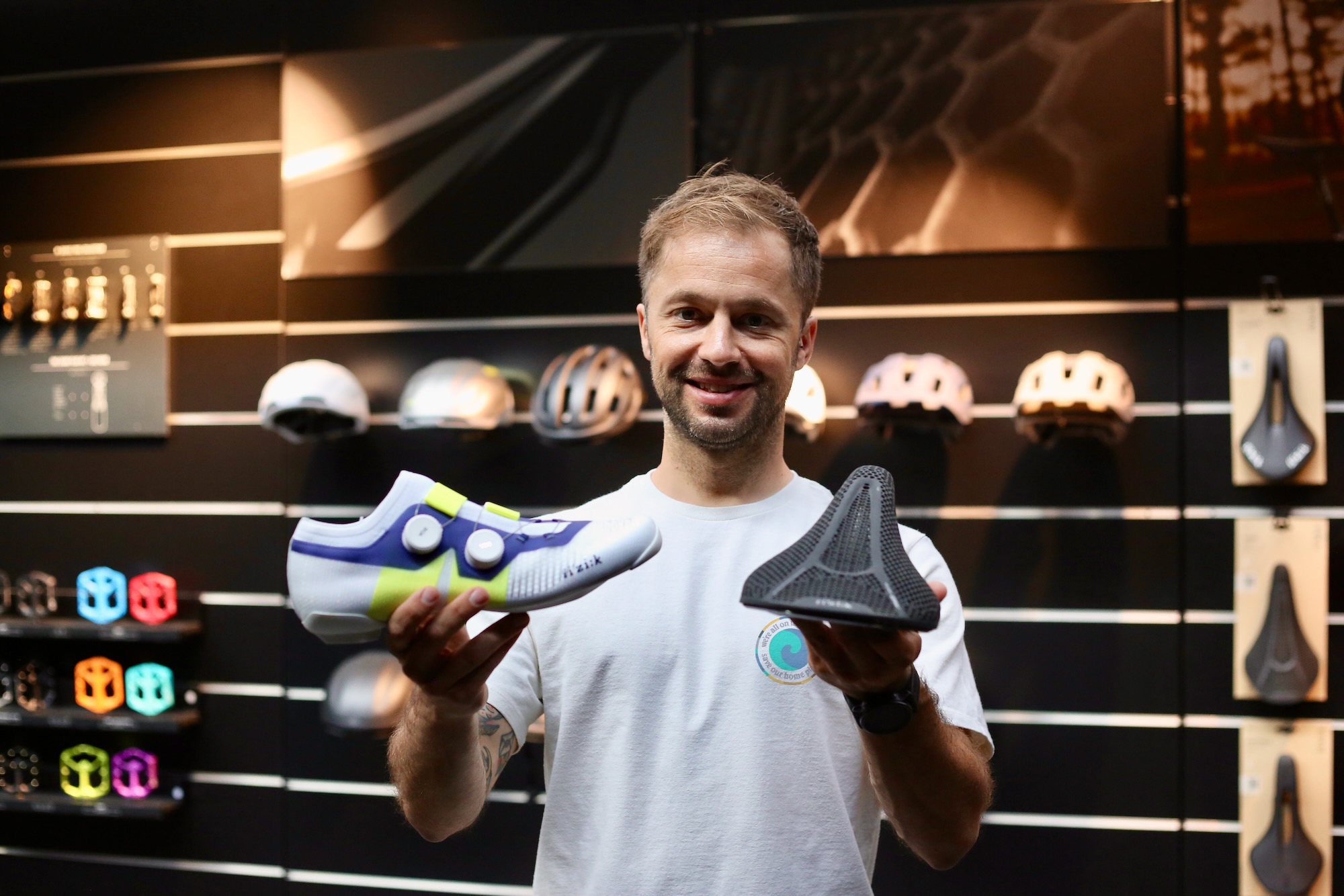
筆者を迎えてくれたニコラ・ポレッティ氏。フィジークのグローバルビジネスマネージャーを務める photo:So Isobe
洗練された本社ビルの扉をくぐると、そこは光と影を巧みに組み合わせたモダンな空間が広がっている。「僕の仕事は、フィジークブランドのことを、もっと世界中の人に知ってもらうこと。日本からはるばるきてくれて嬉しいよ」と言う、フィジークのAM Global Business Managerを務めるニコラ・ポレッティ氏が迎えてくれた。
技術と手作業が共存する生産の舞台裏
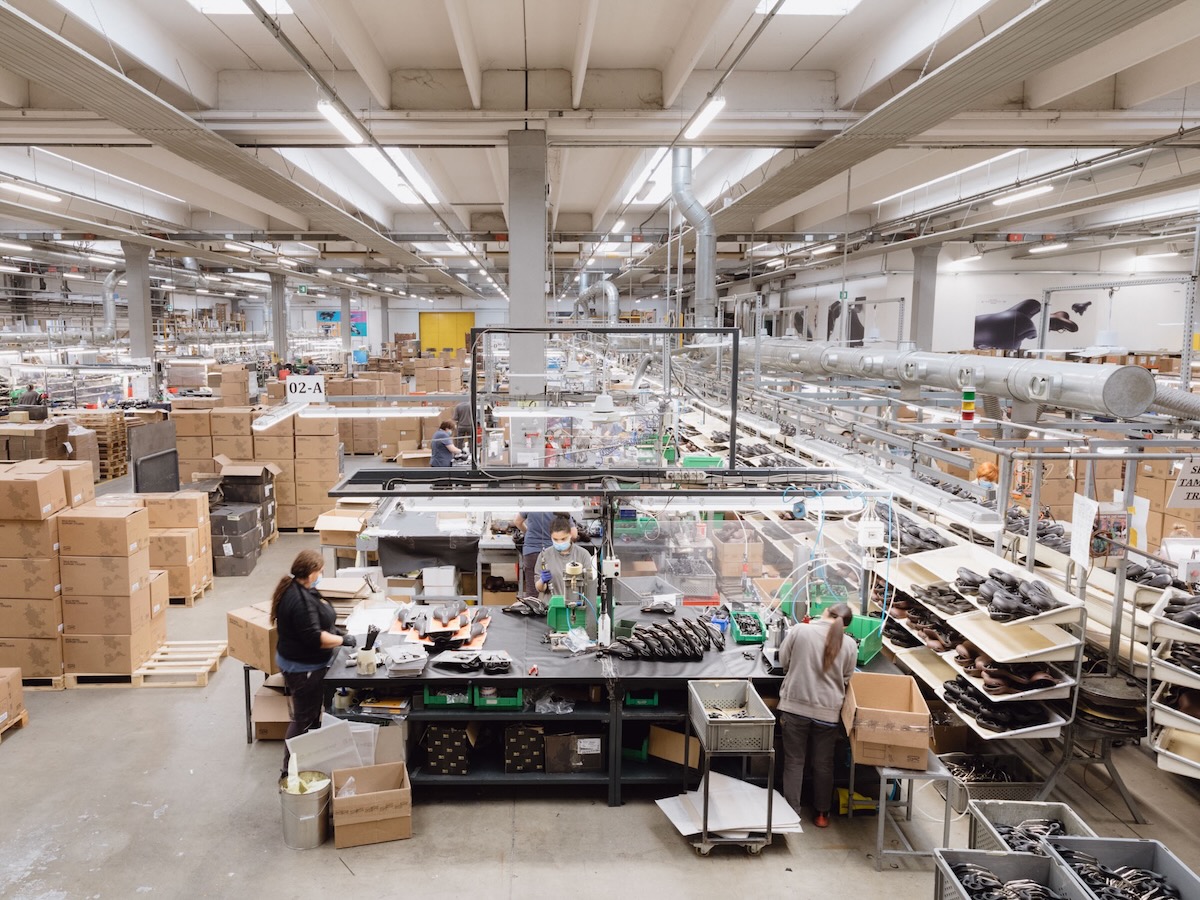
本社裏側にはセラロイヤルとフィジークのサドルを製造する工場が広がっていた (c)Fizik
何度も増築を繰り返してきたという本社裏手のサドル工場は、まさに圧巻の一言だった。
ガチャガチャ、ゴウゴウ、プシュー...。様々な音が鳴り響く空間内では、成型から、仕上げ、品質管理に至るまで、すべてを自社内で完結する一貫生産体制が整えられている。シティユース向けのサドルは海外拠点でも生産されているが、特に品質管理が重視されるフィジークのサドルはこの場所でのみ製造されている(撮影禁止だったのが非常に残念だ)。
サドルの製造自体は、多くの工業製品と同様、ラインによって進められる。建屋内にはジェットコースターのような製造ラインが縦横無尽に駆け巡り、その上をサドルやベース金型がひっきりなしに流れていく。ベースの成形、フォーム素材との貼り合わせ、表皮の接着、最終的な仕上げ処理──。工程を経るごとに、「素材」が少しずつ「製品」としての形を帯びていく。
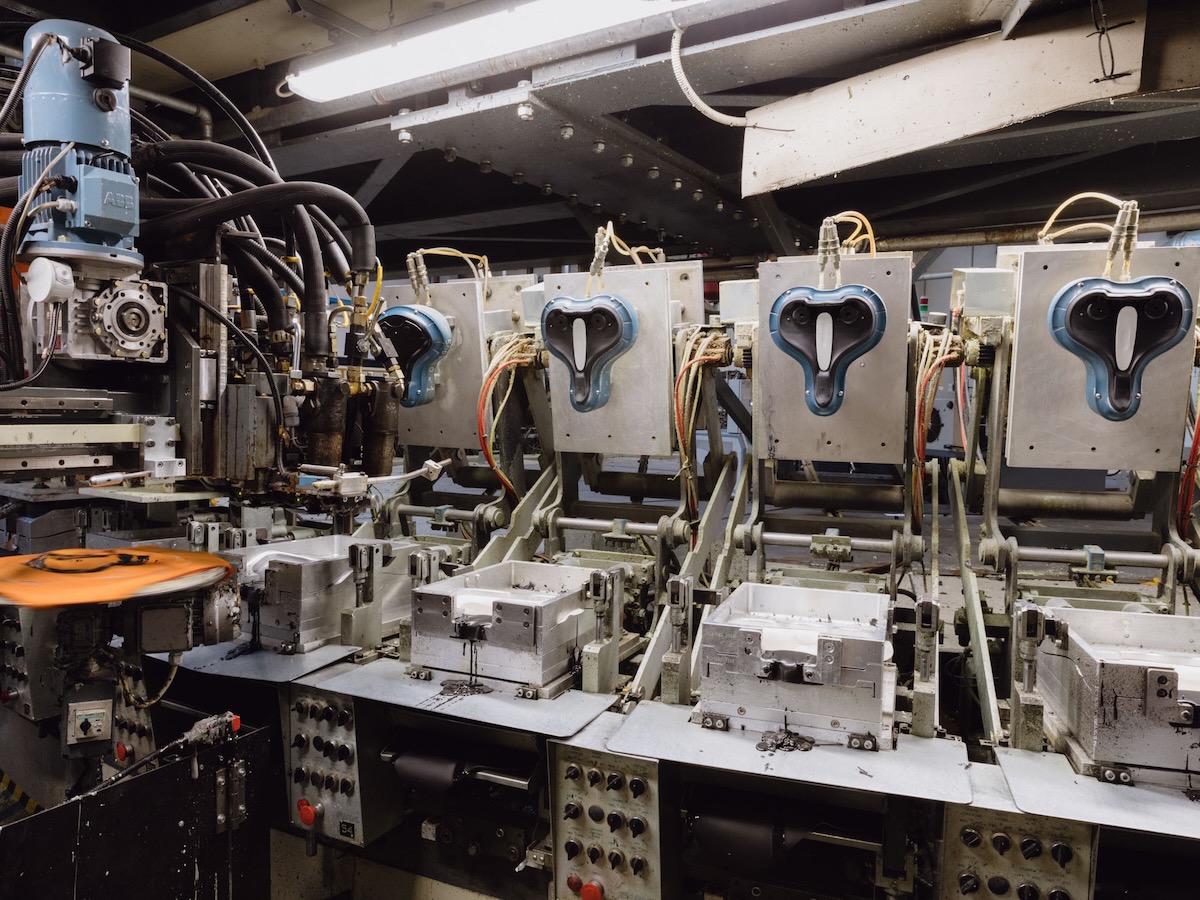
サドル製造のスタート地点はベース製造から。続いてベースにフォームが貼り付けられていく (c)Fizik 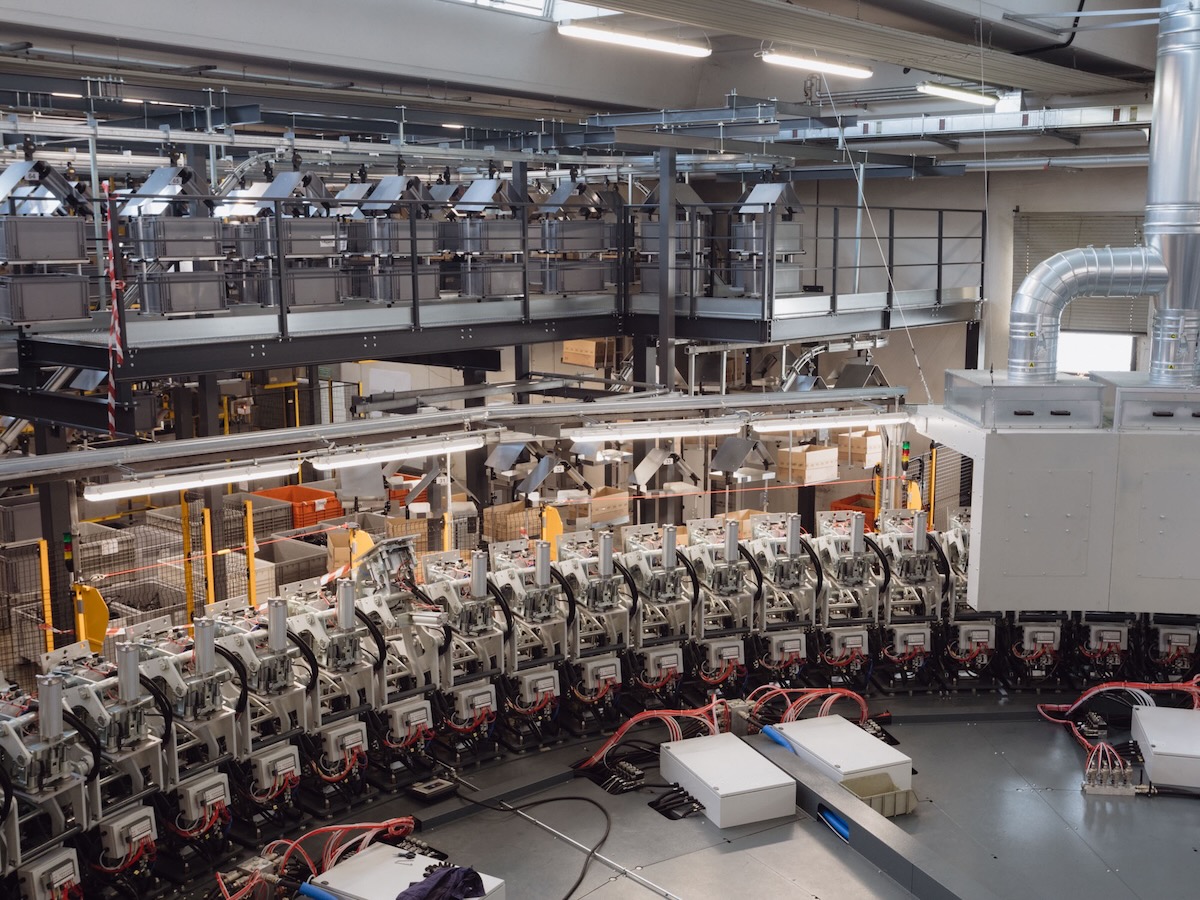
回転するライン。さまざまな段階で様々な部品が追加され、製造工程が進んでいく (c)Fizik
だが、フィジークのサドルが他のシティユース製品と決定的に異なるのは、工程の随所に熟練職人の手作業が残されている点だ。表皮の貼り付け、カーボンレールとベースの接着、そして最終的な品質チェックに至るまで、実のところ、製造工程の多くが手作業によって支えられている。
「イタリアの職人が、イタリアの本社工場で手作業することに意味がある。それこそが高級ブランドとして最も大切にしていることなんだ」と、ポレッティ氏は語る。もちろん効率やコストだけを優先すれば、すべての工程を外注するという選択肢もある。しかしそれでも、自分たちの手で作り上げる「手間」にこそフィジークのDNAが宿っているのだ。
工場内を案内されながら奥へ進むと、少し隔離された一室に大型の3Dプリンターが静かに佇んでいた。ここでは、フィジークがいち早く手がけたAdaptiveサドルの3Dプリントパッドが成形されている。残念ながら取材時には稼働していなかったが、すべてのプロセスがこの場所で完結しているという事実は、それだけでも印象的だった。
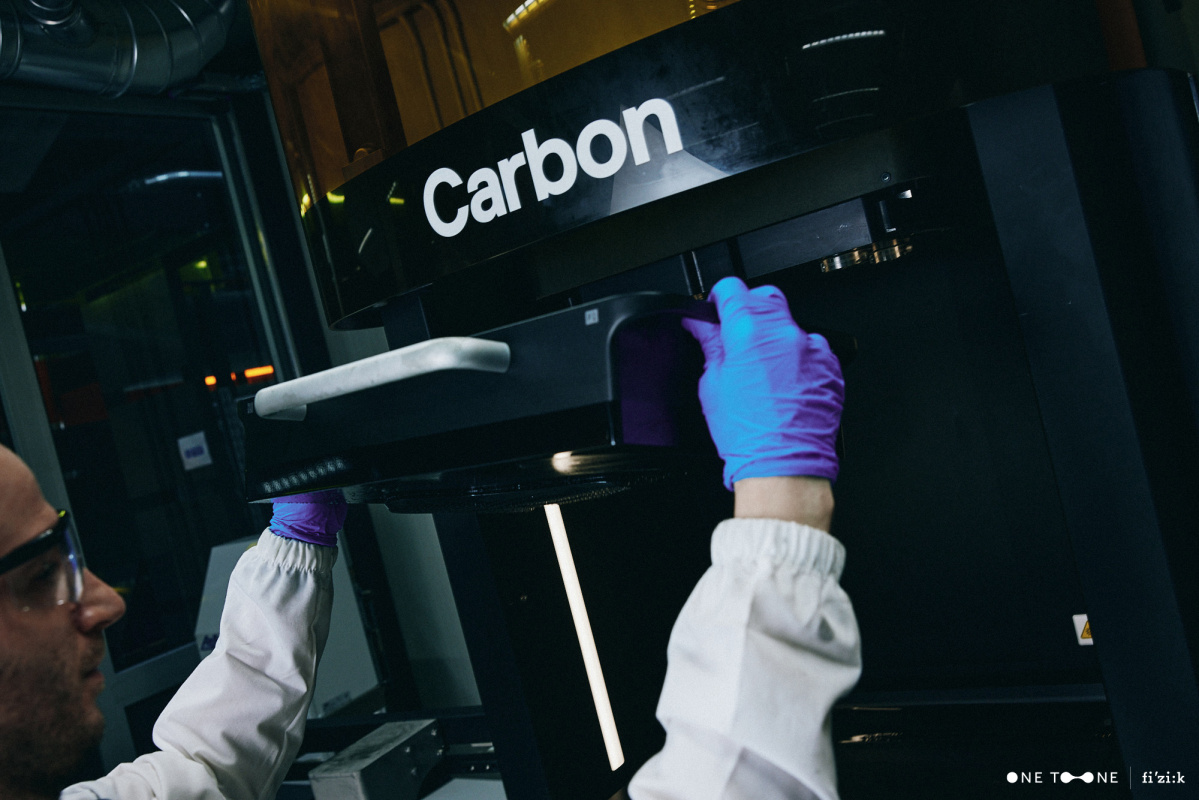
隔離された場所にはカーボン社の3Dプリンターが2基鎮座していた(当日は稼働していなかったが...) (c)カワシマサイクルサプライ
「今やいろいろなブランドから3Dプリントサドルが出てきましたが、我々から見ると、"ただ3Dプリントパッドをつけただけ"のサドルも少なくありません。形状を緻密にコントロールし、サドルの各部分に求められる機能をしっかりと与えているのは、我々がいかにこだわって開発しているかの証拠です」とポレッティ氏の言葉には自信が溢れる。
プリンタールームの隣には、様々な機械が忙しなく動くテストルームがあった。サドルの耐圧試験や、表皮の傷つきテストをしたり、その項目は様々。プロトタイプはもちろん、すでに市販されている製品も、週に1回はラインから完成品を抜き取って検査機にかけているそうだ。
機械の音が響く工場の奥に、確かに息づいていた職人たちの手と眼。高品質なサドルが生まれる現場の背景には、製品設計とブランド戦略を担う明確な思想がある。その核を知るべく、ポレッティ氏へのインタビューを行った。
言葉で紐解く、フィジークのものづくり哲学
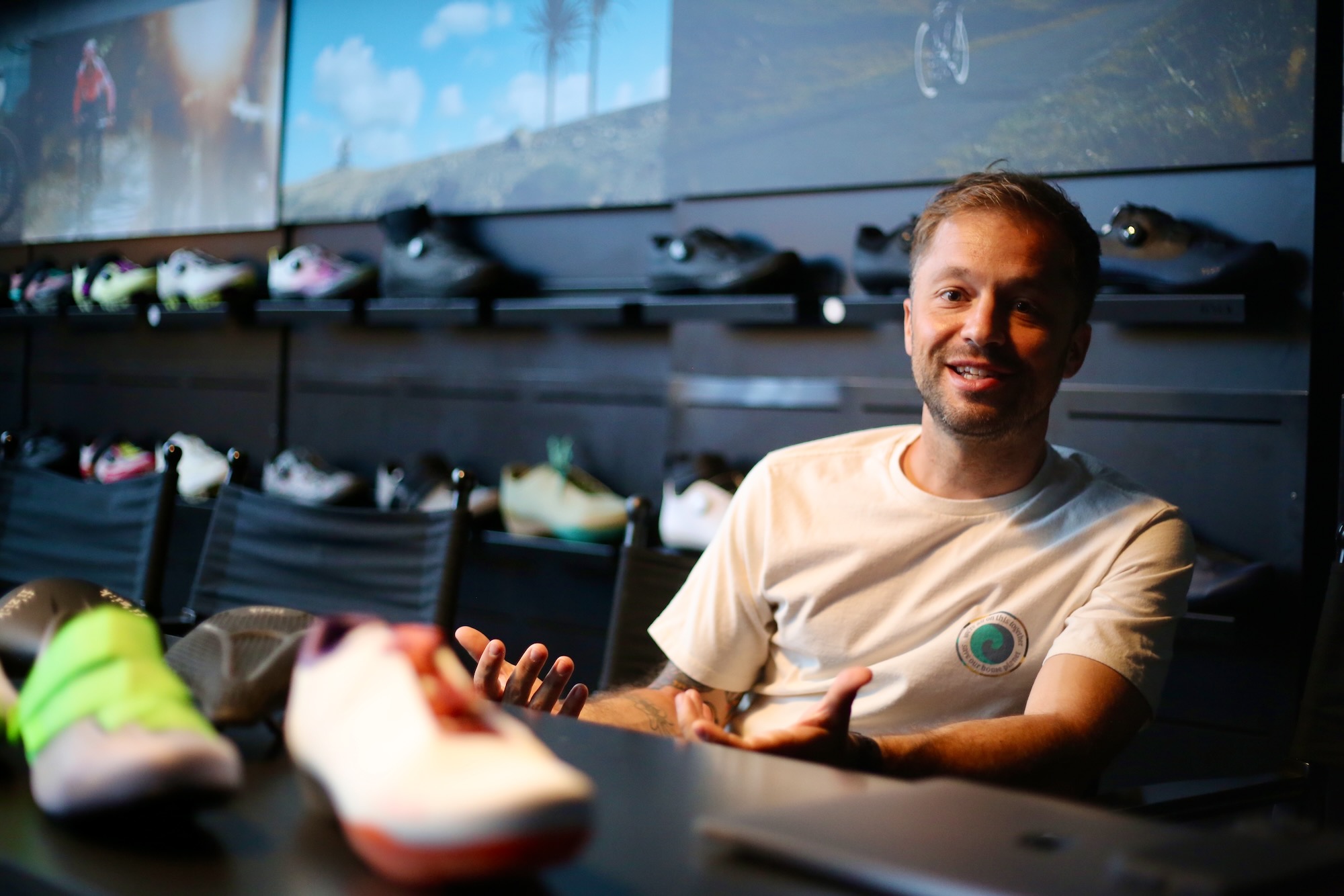
工場見学を終え、ポレッティ氏に話を聞いた。フィジークの哲学やモノづくり、最新のプロダクトについて深掘りした photo:So Isobe
今回紹介した内容の続きは、フィジークの輸入販売を行うカワシマサイクルサプライがスタートさせた深掘りコラム「THE ANSWER」にて公開中。ポレッティ氏が語る「製品開発の哲学」や「サドルとライダーの関係性」について、より深く掘り下げたインタビューフルバージョンは以下のリンクからチェックしてほしい。
text:So Isobe
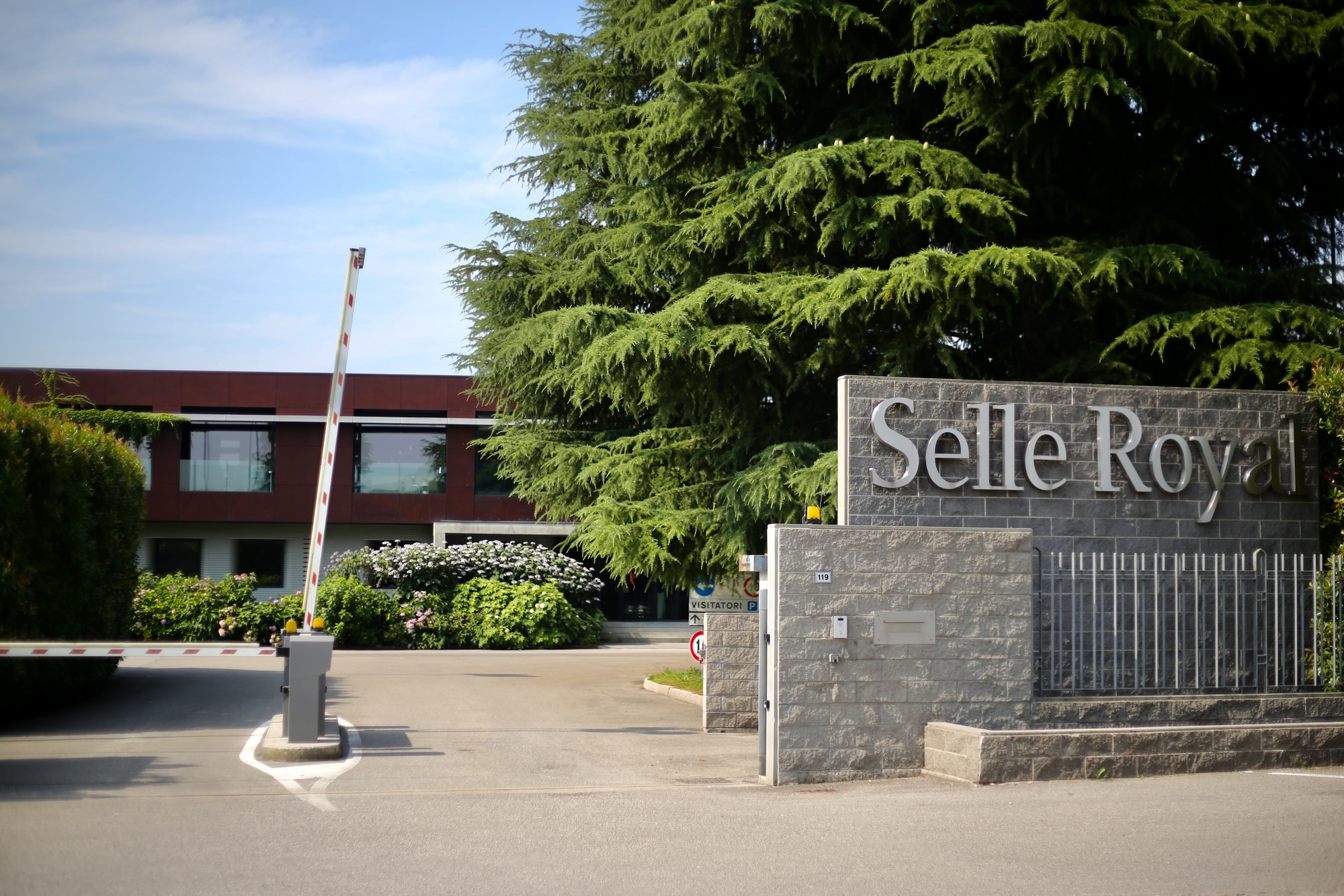
イタリア北部、ヴィチェンツァ郊外の町、ポッツォレオーネ。名だたる名門ブランドがひしめくヴェネト州に、世界中のライダーから愛されるブランド「フィジーク」、そしてその親会社であるセラロイヤルグループの本社はある。
周囲に広がるのは、穏やかな農村風景と点在する工場群。高い建物はほとんどなく、空はどこまでも高く広い。訪れたこの日も、ヴェネト平野らしい開放感に包まれていた。
セラロイヤルの原点は、1956年にリッカルド・ビゴーリンが立ち上げた小さな自転車サドル工房にある。それから約70年。いまや同社は、年間1400万個以上の製品を手がける世界最大級のサドルメーカーへと成長した。ポッツォレオーネは創業当初から変わらずブランドの中枢を担い、現在は本社機能と開発部門、さらにフィジークの高性能サドル製造を担う主要ファクトリーが集約されている。
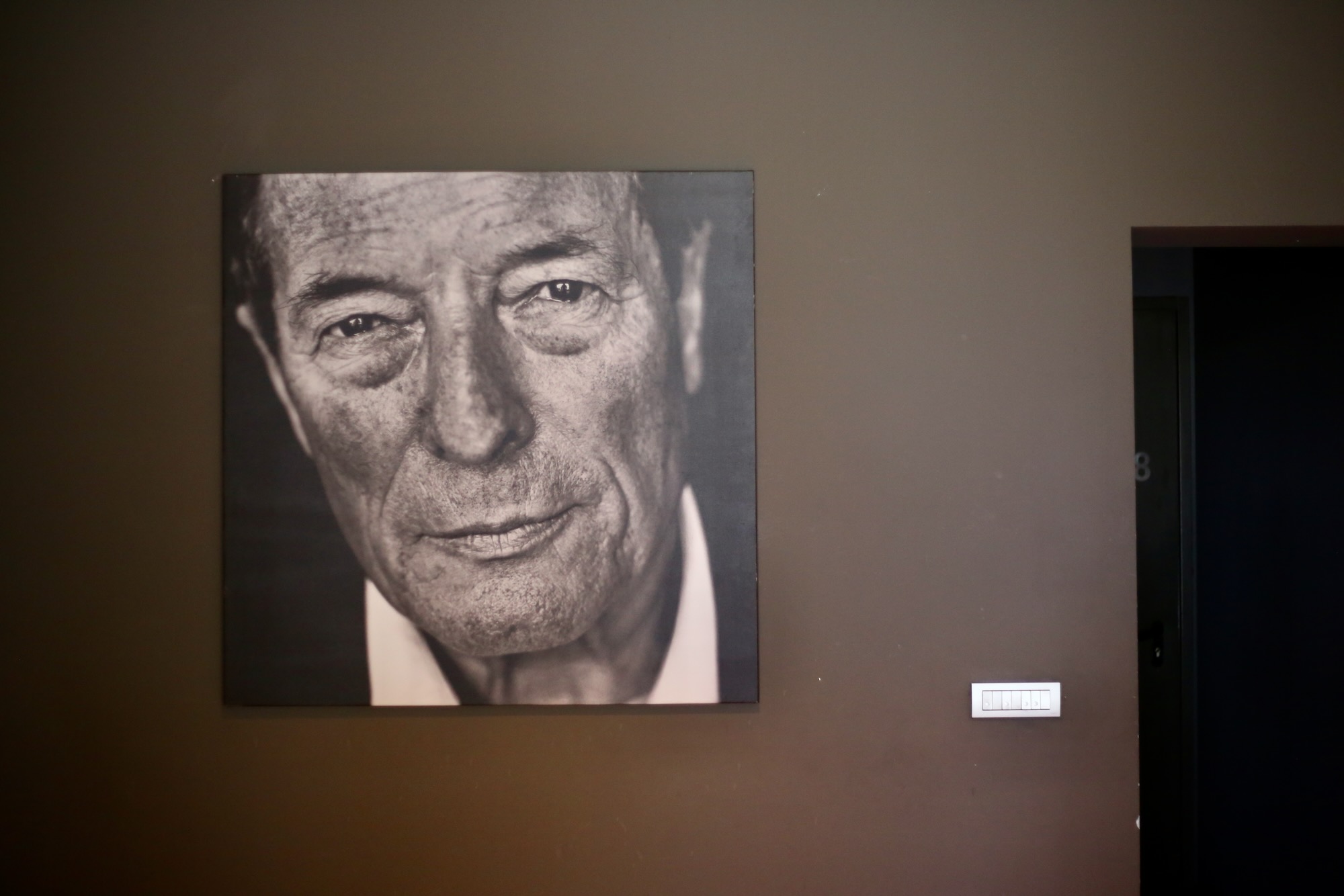
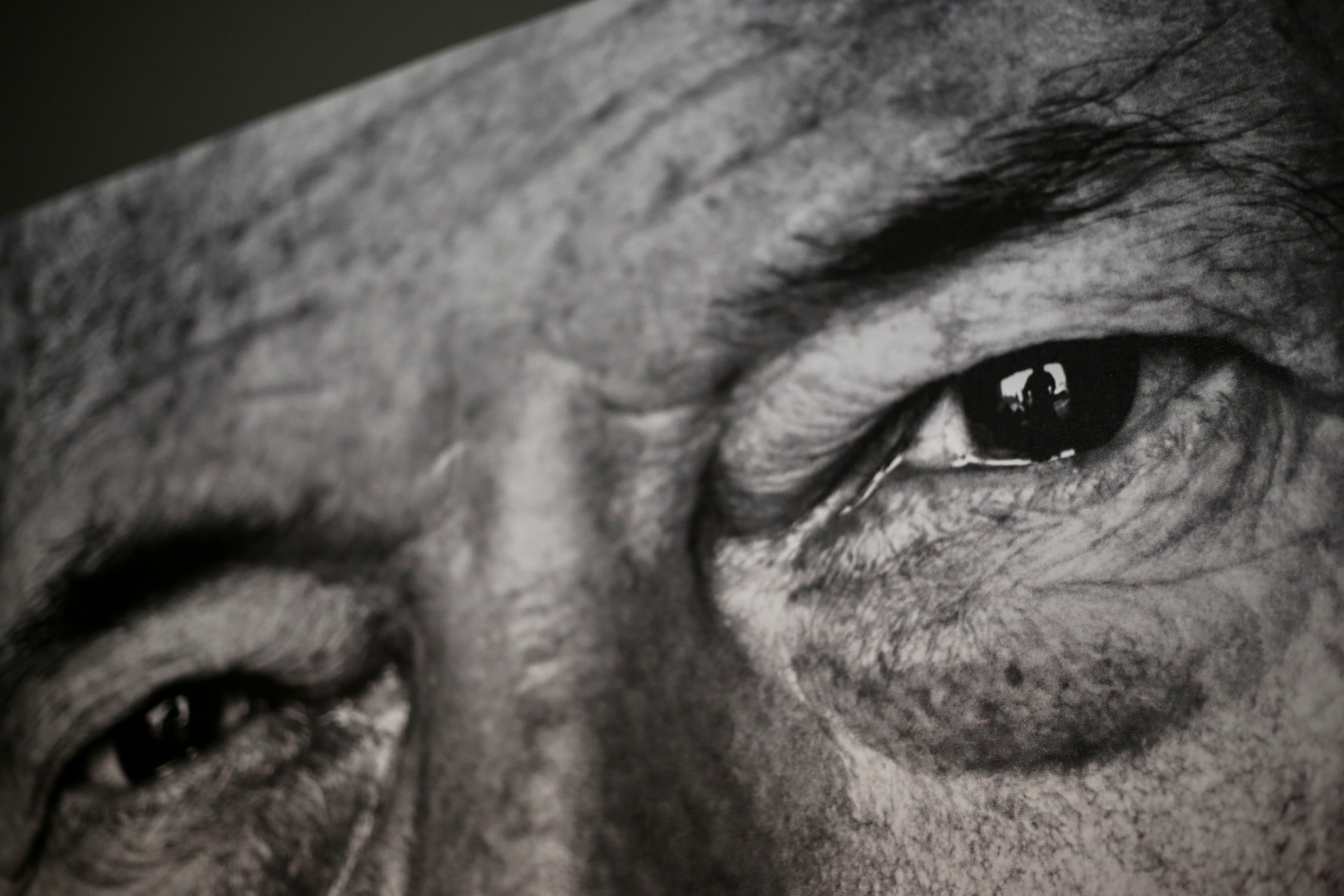
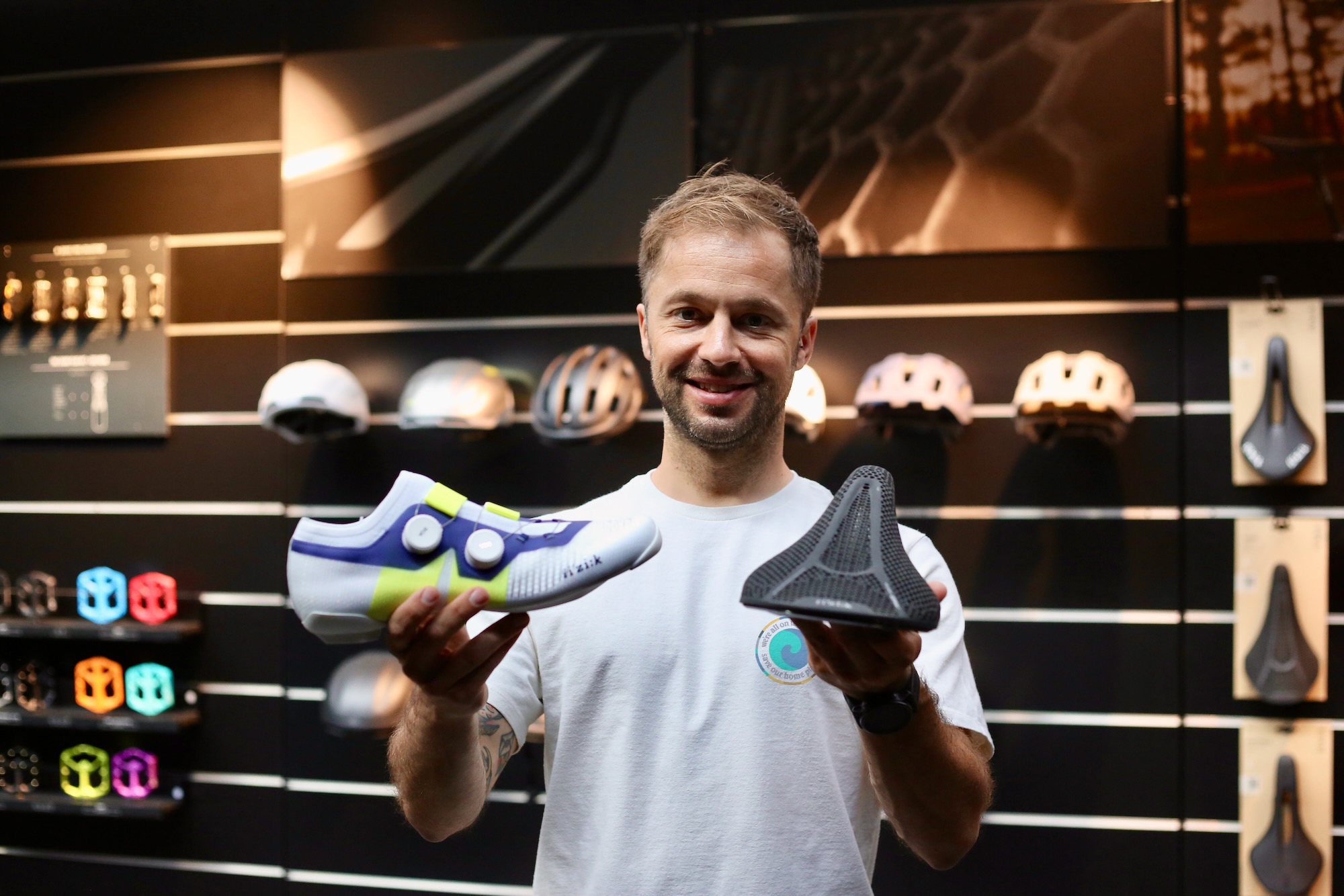
洗練された本社ビルの扉をくぐると、そこは光と影を巧みに組み合わせたモダンな空間が広がっている。「僕の仕事は、フィジークブランドのことを、もっと世界中の人に知ってもらうこと。日本からはるばるきてくれて嬉しいよ」と言う、フィジークのAM Global Business Managerを務めるニコラ・ポレッティ氏が迎えてくれた。
技術と手作業が共存する生産の舞台裏
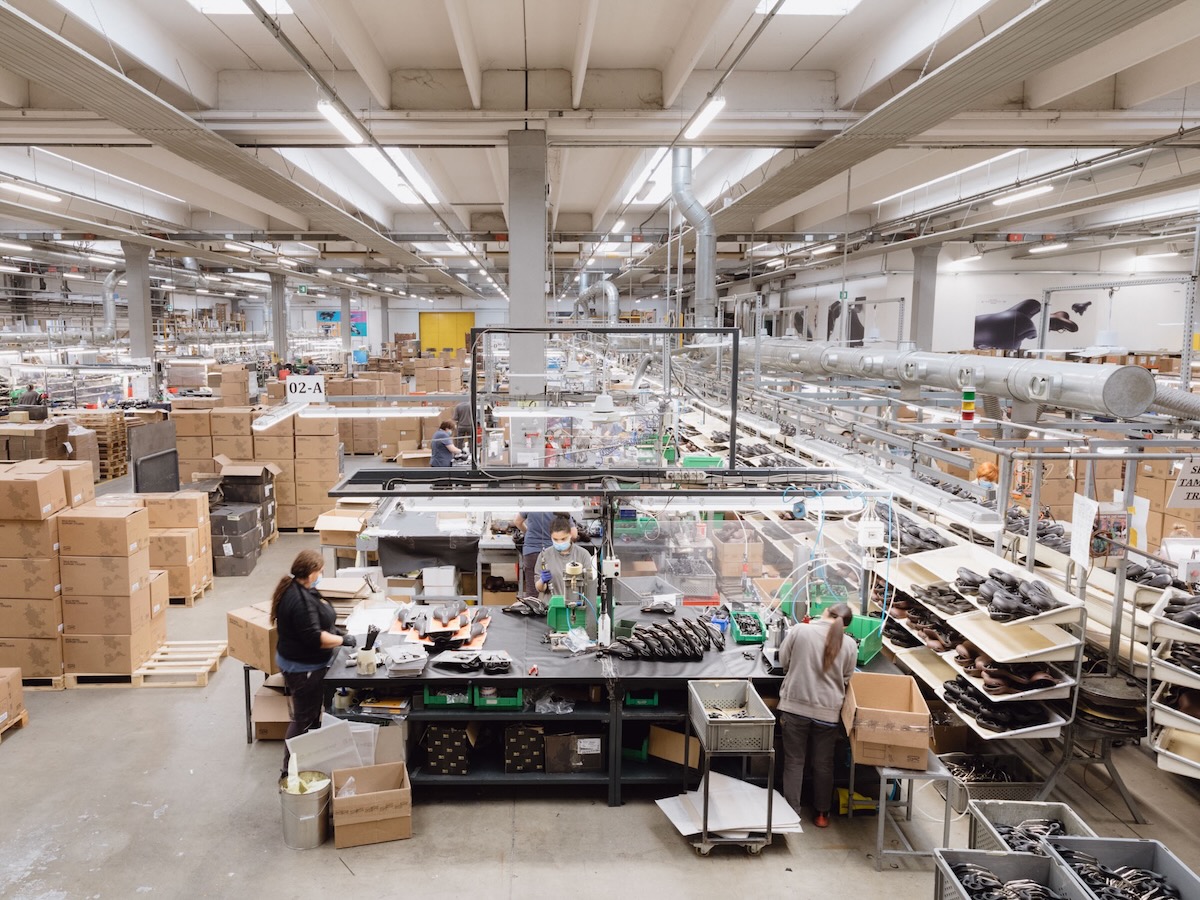
何度も増築を繰り返してきたという本社裏手のサドル工場は、まさに圧巻の一言だった。
ガチャガチャ、ゴウゴウ、プシュー...。様々な音が鳴り響く空間内では、成型から、仕上げ、品質管理に至るまで、すべてを自社内で完結する一貫生産体制が整えられている。シティユース向けのサドルは海外拠点でも生産されているが、特に品質管理が重視されるフィジークのサドルはこの場所でのみ製造されている(撮影禁止だったのが非常に残念だ)。
サドルの製造自体は、多くの工業製品と同様、ラインによって進められる。建屋内にはジェットコースターのような製造ラインが縦横無尽に駆け巡り、その上をサドルやベース金型がひっきりなしに流れていく。ベースの成形、フォーム素材との貼り合わせ、表皮の接着、最終的な仕上げ処理──。工程を経るごとに、「素材」が少しずつ「製品」としての形を帯びていく。
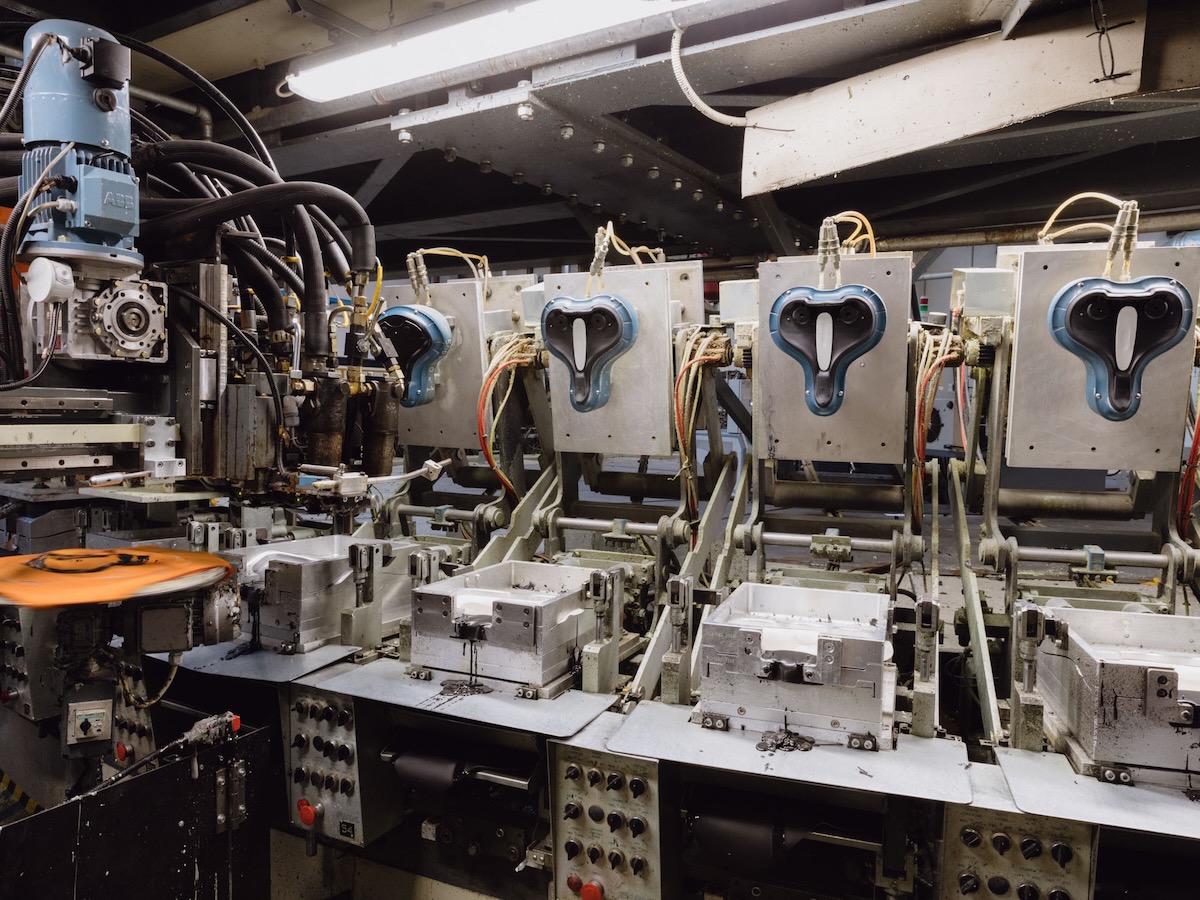
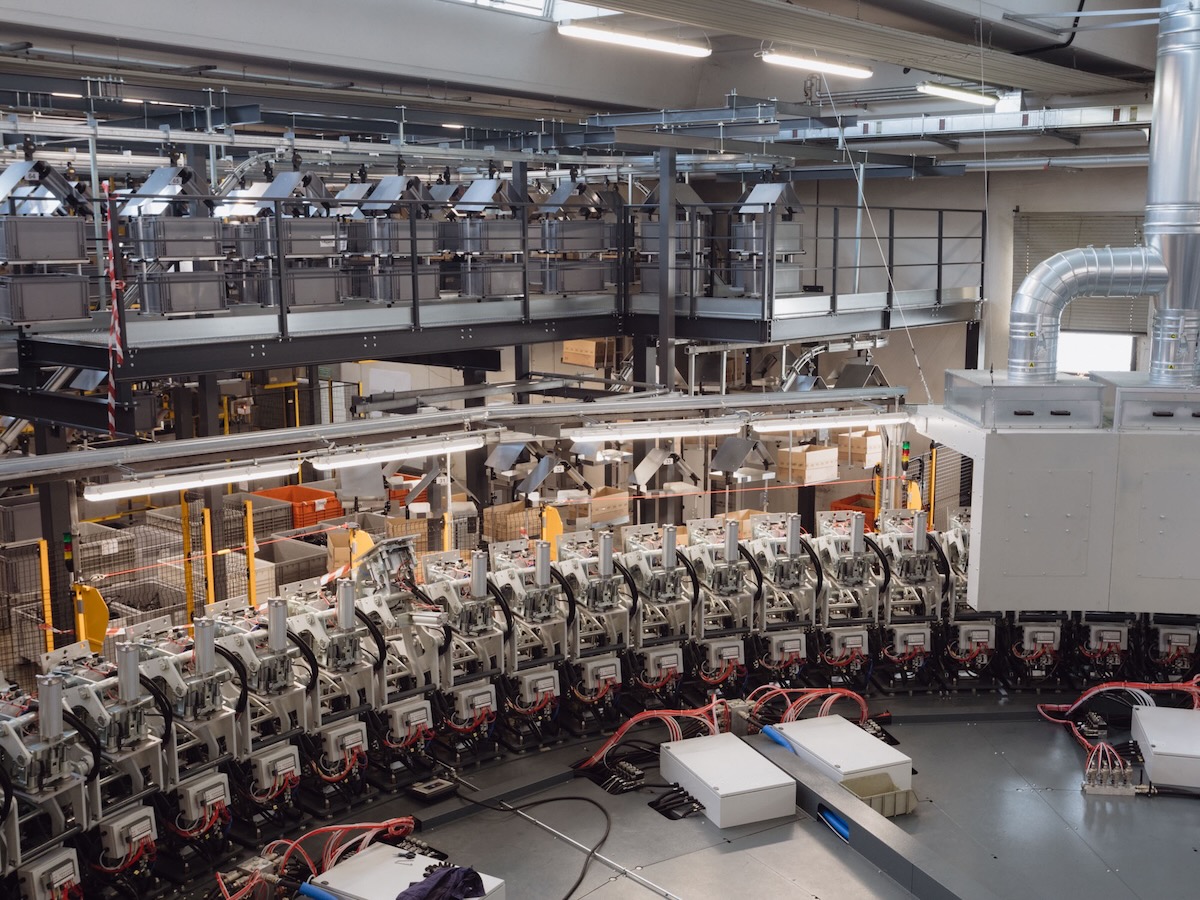
だが、フィジークのサドルが他のシティユース製品と決定的に異なるのは、工程の随所に熟練職人の手作業が残されている点だ。表皮の貼り付け、カーボンレールとベースの接着、そして最終的な品質チェックに至るまで、実のところ、製造工程の多くが手作業によって支えられている。
「イタリアの職人が、イタリアの本社工場で手作業することに意味がある。それこそが高級ブランドとして最も大切にしていることなんだ」と、ポレッティ氏は語る。もちろん効率やコストだけを優先すれば、すべての工程を外注するという選択肢もある。しかしそれでも、自分たちの手で作り上げる「手間」にこそフィジークのDNAが宿っているのだ。
工場内を案内されながら奥へ進むと、少し隔離された一室に大型の3Dプリンターが静かに佇んでいた。ここでは、フィジークがいち早く手がけたAdaptiveサドルの3Dプリントパッドが成形されている。残念ながら取材時には稼働していなかったが、すべてのプロセスがこの場所で完結しているという事実は、それだけでも印象的だった。
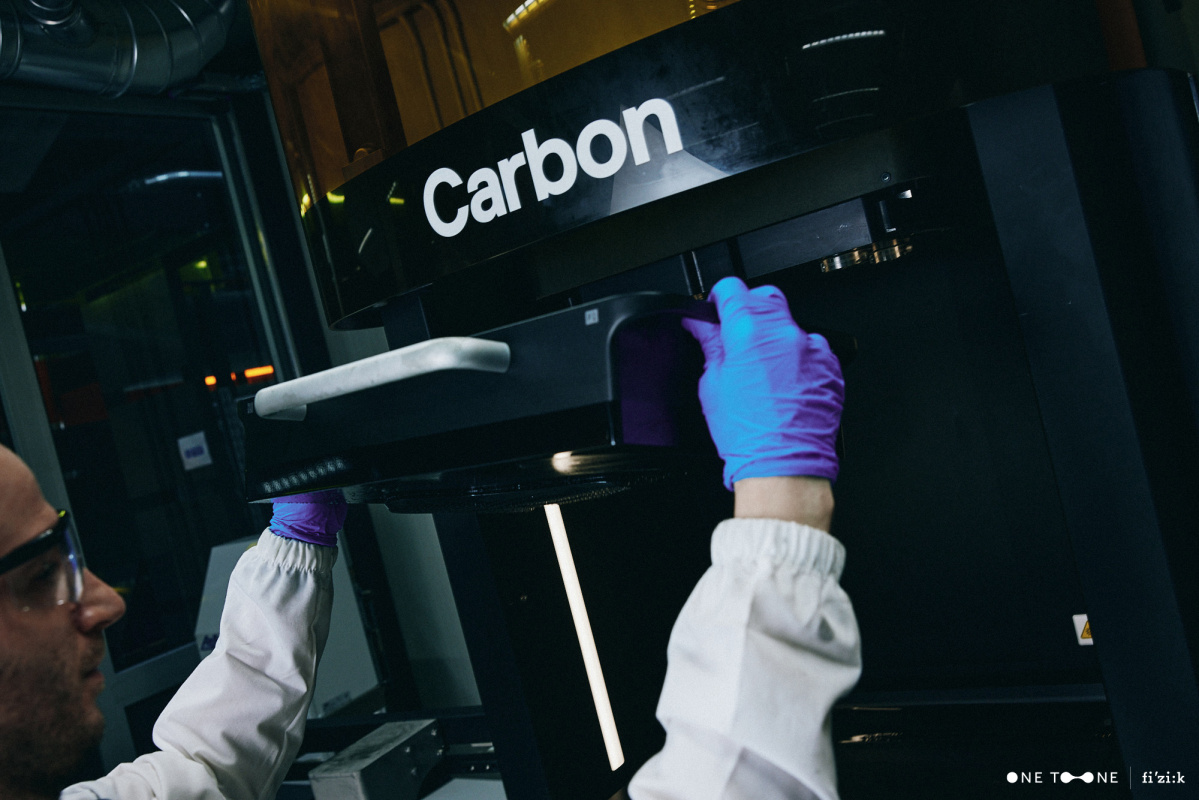
「今やいろいろなブランドから3Dプリントサドルが出てきましたが、我々から見ると、"ただ3Dプリントパッドをつけただけ"のサドルも少なくありません。形状を緻密にコントロールし、サドルの各部分に求められる機能をしっかりと与えているのは、我々がいかにこだわって開発しているかの証拠です」とポレッティ氏の言葉には自信が溢れる。
プリンタールームの隣には、様々な機械が忙しなく動くテストルームがあった。サドルの耐圧試験や、表皮の傷つきテストをしたり、その項目は様々。プロトタイプはもちろん、すでに市販されている製品も、週に1回はラインから完成品を抜き取って検査機にかけているそうだ。
機械の音が響く工場の奥に、確かに息づいていた職人たちの手と眼。高品質なサドルが生まれる現場の背景には、製品設計とブランド戦略を担う明確な思想がある。その核を知るべく、ポレッティ氏へのインタビューを行った。
言葉で紐解く、フィジークのものづくり哲学
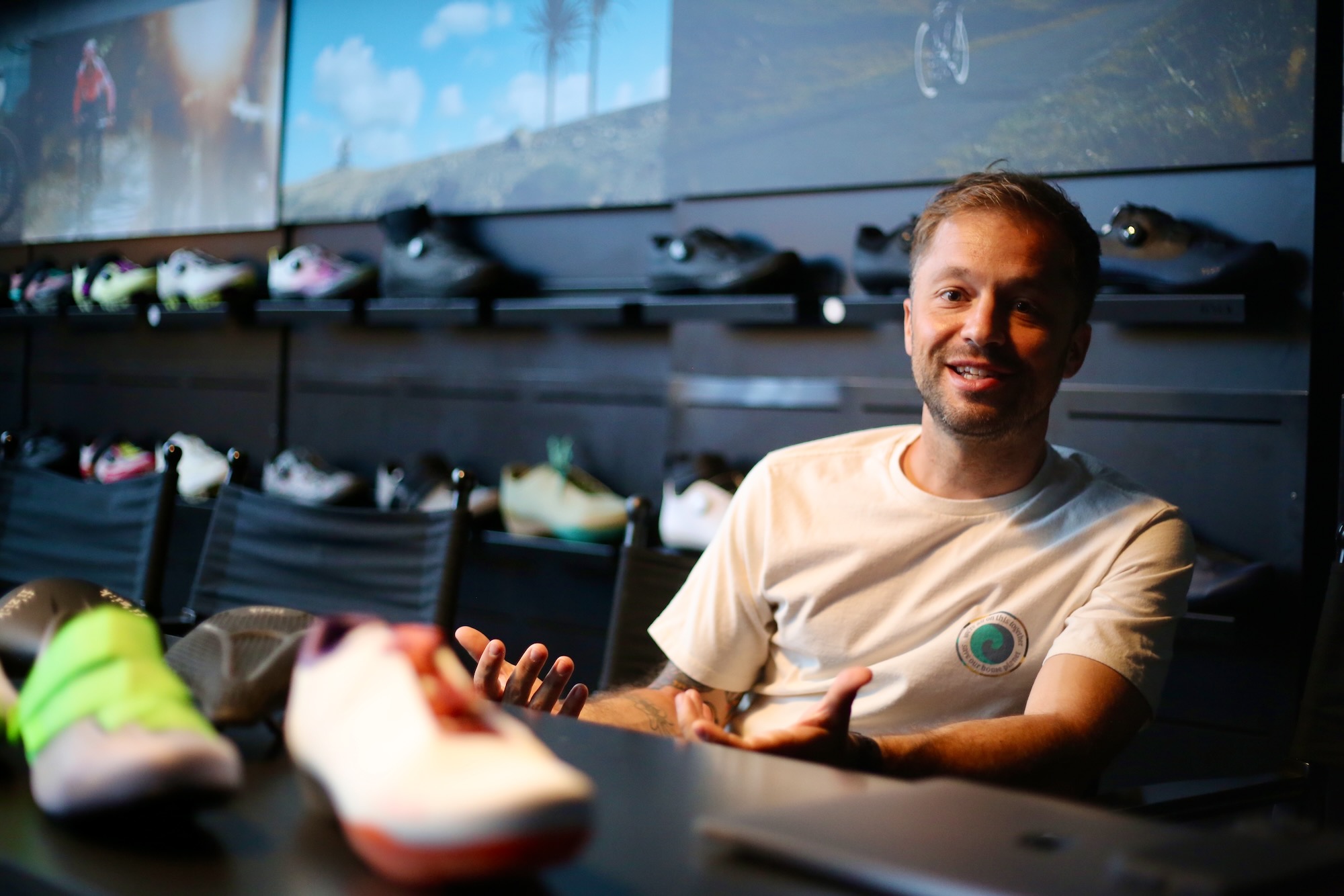
今回紹介した内容の続きは、フィジークの輸入販売を行うカワシマサイクルサプライがスタートさせた深掘りコラム「THE ANSWER」にて公開中。ポレッティ氏が語る「製品開発の哲学」や「サドルとライダーの関係性」について、より深く掘り下げたインタビューフルバージョンは以下のリンクからチェックしてほしい。
text:So Isobe
Amazon.co.jp